Производство бетонной тротуарной плитки методом вибролитья
Технологическая схема производства
Для производства вибролитой тротуарной плитки необходимо нежилое помещение 100-300 кв. м. с удобными подъездными путями. Желательно иметь трехфазное электроснабжение, подвод холодной и по возможности горячей воды, складские площади и навес для хранения готовой продукции (песка, щебня, цемента, добавок, красителей).
Необходимо оборудование: минимум одна бетономешалка (вторая для бетонов с пигментом), один формовочный вибростол (желательно иметь дополнительный расформовочный вибростол), минимум два-три суточных комплекта пластиковых форм, гидравлическую тележку, ванну с подогревом для воды, емкость для промывки форм, вытяжку, вибросито, стеллажи, поддоны.
Процесс производства делится на этапы:
- Подготовка и смазка (при необходимости) пластиковых форм.
- Приготовление бетонной смеси в бетоносмесителе.
- Заполнение смесью пластиковых форм (первый слой – цветной бетон).
- Формование на вибростоле (сначала первый, затем второй слой).
- Выдержка изделий в формах до 48 часов.
- Распалубка (выбивка изделия) форм.
- Маркировка продукции, упаковка.
- Подготовка форм к повторной заливке (очистка, смазка).
ГОСТ 17608-91 «Плиты бетонные тротуарные. Технические условия»
ГОСТ 17608-91 введен 01.01.1992, действует в настоящее время (http://www.gost.ru/wps/portal/pages.CatalogOfStandarts)
Согласно ФЗ «О техническом регулировании» предусматривается добровольная сертификация продукции по инициативе изготовителя. Сертификация подтверждает соответствие продукции определенным требованиям качества и безопасности. Тротуарная плитка не нуждается в обязательной сертификации, однако она должна изготавливаться по ГОСТ 17608-91.
Для производства должен использоваться тяжелый (БСТ) или мелкозернистый бетон (БСМ). Марка бетона по морозоустойчивости – не ниже F300. Водопоглощение плит из тяжелого бетона не должно быть выше 5% и 6% - для мелкозернистого бетона, Прочность на сжатие – в пределах В22,5-В35, истираемость менее 0,7 г/см, водоцементное отношение – не более 0,4. Бетонные смеси должны готовиться с воздухововлекающими добавками с итоговым значением не более 4-5% и с обязательным добавлением пластифицируемых добавок.
Нормируемая отпускная прочность должна составить в холодный период 90% и 70 % в теплое время года. ГОСТ предусматривает толщину плит не менее 50 мм. Тротуарные плиты должны иметь класс не ниже В22,5 и В25.
Таким образом, ГОСТ разделил плиты на типы, стандартизировал плиты по маркам в зависимости от формы плиты и ее типоразмеров, установил правила маркировки и установил состав бетона. Плиты должны быть двухслойные, при этом толщина верхнего слоя – не менее 20 мм, возможен цветной слой.
Состав бетона по ГОСТ 17608-91
- Портландцемент;
- Заполнители:
- В качестве мелкого заполнителя используют природные, или обогащенные и дробленые пески, со значением крупности от 2,2, а для тяжелого – более 2,0;
- В качестве крупного заполнителя используют щебень из природного камня, доменного шлака, гравия. Максимальный размер частиц крупного заполнителя: не больше 10 мм применяется в плитах толщиной менее 50 мм и 20 мм – в плитах от 50 мм;
3. Бетонные смеси должны готовиться с применением добавок:
- Пластификатор С-3 в объеме (массе) 0,3-0,7 % от массы сухого цемента;
- Воздухововлекающие (объем вовлеченного воздуха не более 4-5%) по массе 0,01-0,02 от массы цемента;
- Пластифицирующие-воздухововлекающие не менее чем 0,02 % от массы цемента;
- Газообразующие в объеме 0,1% от массы сухого цемента;
- Ускоритель твердения раствора (кальций, хлористый в объеме не больше 3 % от массы цемента).
4. Вода;
5. Пигменты для изготовления цветных плит.
Примерные нормы расхода материалов
Для изготовления бетонных тротуарных плит без красителя рекомендуются следующие пропорции состава бетонной смеси:
- портландцемент марки «марка М 500-Д0» - 23% (кг от общей массы сухой смеси);
- гранитный щебень фракции 10-20 мм - 57% (кг от общей массы сухой смеси);
- речной песок - 20% (кг от общей массы сухой смеси);
- пластификатор по рецепту изготовителя (С-3 или другой -0,2-0,7% (от массы цемента));
- воздухововлекающая добавка 0,02 %
- ускорители твердения – от 0,6 до 3%
- вода - 30- 40% (от объема цемента);
- волокна полипропиленовые, полиамидные или стеклянные L= 5-20 мм, d= 5-50 мкм – 0,7-1,0 кг на 1 кубометр бетона.
В цветную плитку дополнительно добавляются пигменты в количестве:
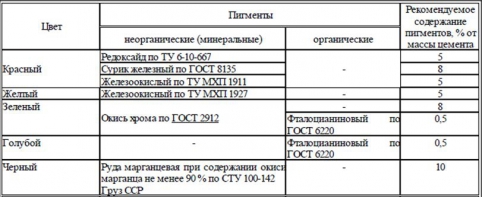
Соотношение воды и бетона влияет на прочность готовой продукции. Влаги в бетонной смеси должно быть 30-40% от общего содержания цемента. Увеличение нормы пигмента уменьшает прочность бетона.
Еще один вариант примерных соотношений основных компонентов для получения качественной смеси:
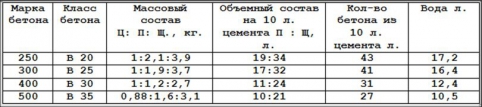
Приготовление бетонной смесиДля приготовления раствора нужно изучить состав бетона, подготовить все компоненты, соблюдать очередность добавления компонентов в бетоносмеситель. Сначала заливают не весь объем воды, а только значительную ее часть, затем добавляются твердые компоненты и оставшаяся вода. Растворяемые добавки, вводятся сразу же с водой затворения. Описанная последовательность закладки компонентов неслучайна. Если сначала закинуть цемент, а потом щебень и воду, то цемент начнет налипать и не распределится равномерно по объему.
Алгоритм действий для гравитационного бетоносмесителя:
- Включается бетоносмеситель.
- Заливается вода чуть меньше выбранной нормы затворения.
- Засыпается 1/2 часть необходимого количества щебня.
- Добавляются заранее приготовленные добавки и пластификатор.
- Засыпается весь цемент.
- Добавляется весь песок.
- Добавляются полиамидные волокна.
- Засыпается оставшийся щебень.
- Доливается остаток воды.
Если в составе бетона есть полипропиленовые и щелочестойкие стекловолокна, то они вводятся одновременно с водой; а если необходимы полиамидные волокна, то их вводят на последнем этапе в практически готовую смесь. Как вариант, вместо обычной воды в смесь сразу добавляется раствор суперпластификатора.
При приготовлении цветного бетона с использованием красителей применяется послойное формирование изделия в формах. В этом случае используют два бетоносмесителя разного объема, так как составы компонентов лицевого и основного слоя по соотношению неодинаковы. Замешиваем бетон с красителем в меньшем по объему бетоносмесителе (для экономии пигментов), а в большем бетоносмесителе – без красителя. Пигмент и пластификатор добавлять в начале процесса загрузки бетоносмесителя, растворив их в затворяющей воде.
На однородность раствора, влияет продолжительность перемешивания, особенность устройства барабана бетоносмесителя, вид заполнителей, их крупность, подвижность смеси и содержание вяжущего. Продолжительность перемешивания бетона составляет 3-3,5 минуты.
Ориентировочный режим смешивания компонентов смеси в гравитационных смесителях малой вместительности (менее 750 литров) по ГОСТ 7473-2010:
- Вода + 1/2 щебня – 15-20 с.;
- вода, 1/2 щебня + добавки, пластификатор – 5-10 с.;
- вода, 1/2 щебня, добавки, + цемент – 15-20 с.;
- вода, 1/2 щебня, добавки, цемент + песок – 15-20 с.;
- вода, 1/2 щебня, добавки, цемент, песок + волокна полиамида - 30-50 с.;
- вода, 1/2 щебня, добавки, цемент, песок, волокна + остатки щебня – 15-20 с.;
- вода, все добавки, цемент, песок, вся щебень + остатки воды – 30-55 с.;
- итоговое время: – 3-3,5 минуты.
Виброформование изделий
Технология вибролитья изделий позволяет получить тяжелый бетон, если в качестве заполнителя используется щебень. Высокочастотная вибрация вытесняет из структуры бетона пузырьки воздуха и воду. Бетонная смесь самоуплотняется на вибростолах в полипропиленовых формах.
Вибростол как и большинство строительного оборудования которое можно взять в аренду на
https://www.pmg.su/ представляет собой станину, на которую сверху при помощи пружин крепится подвижная металлическая столешница с ограждением по периметру. К станине ниже столешницы крепится вибратор.
Плитка должна состоять из двух слоев. Лицевой первый слой задает характеристики прочности и внешний вид, а второй определяет необходимую толщину изделия. Если нужна цветная плитка, то для первого лицевого слоя используют бетонную смесь с красящими пигментами.
Этапы процесса формования:
- Формы раскладывают на вибростоле как можно плотнее, без зазоров.
- Равномерно выкладываем на дно форм первый слой цветного бетона, при этом толщина слоя составляет 2,0-2,5 см. Если нужна серая плитка, то краситель в бетонную смесь не кладут.
- Запускаем вибростол, устанавливаем среднюю амплитуду вибрации. Формы вибрируют в течение 15-20 секунд. Бетонная смесь начинает расплавляться, равномерно покрывая дно пластиковой формы.
- Закладываем второй слой без пигмента, заполнив формы раствором до верха.
- Включить вибратор на 20-40 секунд. Амплитуда колебаний площадки столешницы вибростола - средняя, бетон должен уплотняться, вытесняя воздух и воду, но не закипать. Вибрация должна быть одинаковой на любом участке поверхности. В заготовках могут появляться неровности, которые необходимо заполнять при помощи кельмы бетонщика до краев или срезать лишнее, выравнивая высоту раствора по краю формы.
- Выключить вибратор, при появлении белой пленки на поверхности: это сигнал того, что процесс удачно завершен. После этого остается тщательно загладить поверхность изделия. При нехватке бетона в форме подложить смесь и затереть, добиваясь гладкой и ровной поверхности.
- Изделия в формах отправляются на твердение.
Режим твердения изделий
Твердение (тепловлажностная обработка) изделий следует проводить при температуре не выше 70°С в мягком режиме твердения. Предельная скорость повышения и понижения температуры – не более 25°C в час.
Формы с продукцией перекладываются на поддоны слоями, каждый слой переложить листом пластика по размеру поддона, количество слоев от трех до десяти. Высота слоев зависит от прочности материала формы. На небольших производствах формы укладывают друг на друга штабелями высотой до 10 единиц. Слоеный «пирог» на поддоне перевозится в отведенное для сушки помещение. Поддоны укладывают на ровную чистую поверхность без уклона. Уклон в 1-2 градуса нарушит геометрические формы твердеющих плиток. Поддоны сверху накрыть (штабеля укутать) полиэтиленовой пленкой защитив от высыхания. Поддоны с формами нельзя передвигать ранее, чем пройдет положенное по технологии время твердения (18-48 часов после процесса заливки). Время твердения продукции зависит от температуры помещения и использованных добавок.
Температура твердения плитки должна быть не менее 15 градусов. После завершения твердения готовую плитку извлекают из формы. Для облегчения процесса и продления срока эксплуатации пластиковых форм необходимо формы с изделиями погрузить в термованну с горячей водой на 3-5 минут. Первоначальная температура воды в емкости –
70 – 80 градусов, перед выемкой температура снижается до 35-45°С. Необходимый температурный режим поддерживается электротенами. За время нахождения в ванной форма из полимера, прогреваясь, расширяется на большую величину, чем бетонное изделие. Вынутую форму с плиткой переворачивают донышком вверх и кладут на рядом стоящий расформовочный вибростол. Готовое изделие выскакивает из формы от воздействия вибрации, либо его высвобождают на распалубочном столе, применяя специальные приспособления. Вынутую плитку выставляют на европоддоны лицевой частью друг к другу, обвязывают проволокой или упаковочной лентой, оборачивают стрейч-пленкой и отправляют на хранение. Формы промываются в солевом растворе или 7-10%-растворе соляной кислоты, прополаскиваются, сушатся, смазываются.
Отпуск готовых плит возможен при остижении изделиями 90% прочности в зимнее время года, и 70% - в летний период. Зимой, как правило, ждут 25-28 дней, летом – приблизительно 7 дней с момента изготовления
29/03/2015, 09:03
Производство бетонной тротуарной плитки методом вибролитья
Необходимо оборудование: минимум одна бетономешалка (вторая для бетонов с пигментом), один формовочный вибростол (желательно иметь дополнительный расформовочный вибростол), минимум два-три суточных комплекта пластиковых форм, гидравлическую тележку, ванну с подогревом для воды, емкость для промывки форм, вытяжку, вибросито, стеллажи, поддоны.
ГОСТ 17608-91 «Плиты бетонные тротуарные. Технические условия»
ГОСТ 17608-91 введен 01.01.1992, действует в настоящее время (http://www.gost.ru/wps/portal/pages.CatalogOfStandarts)
Согласно ФЗ «О техническом регулировании» предусматривается добровольная сертификация продукции по инициативе изготовителя. Сертификация подтверждает соответствие продукции определенным требованиям качества и безопасности. Тротуарная плитка не нуждается в обязательной сертификации, однако она должна изготавливаться по ГОСТ 17608-91.
Для производства должен использоваться тяжелый (БСТ) или мелкозернистый бетон (БСМ). Марка бетона по морозоустойчивости – не ниже F300. Водопоглощение плит из тяжелого бетона не должно быть выше 5% и 6% - для мелкозернистого бетона, Прочность на сжатие – в пределах В22,5-В35, истираемость менее 0,7 г/см, водоцементное отношение – не более 0,4. Бетонные смеси должны готовиться с воздухововлекающими добавками с итоговым значением не более 4-5% и с обязательным добавлением пластифицируемых добавок.
Нормируемая отпускная прочность должна составить в холодный период 90% и 70 % в теплое время года. ГОСТ предусматривает толщину плит не менее 50 мм. Тротуарные плиты должны иметь класс не ниже В22,5 и В25.
Таким образом, ГОСТ разделил плиты на типы, стандартизировал плиты по маркам в зависимости от формы плиты и ее типоразмеров, установил правила маркировки и установил состав бетона. Плиты должны быть двухслойные, при этом толщина верхнего слоя – не менее 20 мм, возможен цветной слой.
Состав бетона по ГОСТ 17608-91
5. Пигменты для изготовления цветных плит.
Примерные нормы расхода материалов
Для изготовления бетонных тротуарных плит без красителя рекомендуются следующие пропорции состава бетонной смеси:
В цветную плитку дополнительно добавляются пигменты в количестве:
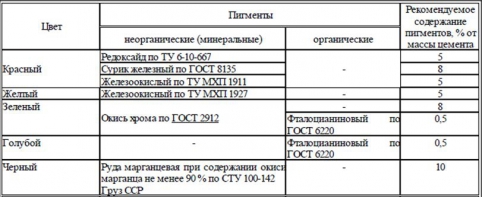
Соотношение воды и бетона влияет на прочность готовой продукции. Влаги в бетонной смеси должно быть 30-40% от общего содержания цемента. Увеличение нормы пигмента уменьшает прочность бетона.Еще один вариант примерных соотношений основных компонентов для получения качественной смеси:
Для приготовления раствора нужно изучить состав бетона, подготовить все компоненты, соблюдать очередность добавления компонентов в бетоносмеситель. Сначала заливают не весь объем воды, а только значительную ее часть, затем добавляются твердые компоненты и оставшаяся вода. Растворяемые добавки, вводятся сразу же с водой затворения. Описанная последовательность закладки компонентов неслучайна. Если сначала закинуть цемент, а потом щебень и воду, то цемент начнет налипать и не распределится равномерно по объему.
Алгоритм действий для гравитационного бетоносмесителя:
Если в составе бетона есть полипропиленовые и щелочестойкие стекловолокна, то они вводятся одновременно с водой; а если необходимы полиамидные волокна, то их вводят на последнем этапе в практически готовую смесь. Как вариант, вместо обычной воды в смесь сразу добавляется раствор суперпластификатора.
На однородность раствора, влияет продолжительность перемешивания, особенность устройства барабана бетоносмесителя, вид заполнителей, их крупность, подвижность смеси и содержание вяжущего. Продолжительность перемешивания бетона составляет 3-3,5 минуты.
Ориентировочный режим смешивания компонентов смеси в гравитационных смесителях малой вместительности (менее 750 литров) по ГОСТ 7473-2010:
Технология вибролитья изделий позволяет получить тяжелый бетон, если в качестве заполнителя используется щебень. Высокочастотная вибрация вытесняет из структуры бетона пузырьки воздуха и воду. Бетонная смесь самоуплотняется на вибростолах в полипропиленовых формах.
Вибростол как и большинство строительного оборудования которое можно взять в аренду на https://www.pmg.su/ представляет собой станину, на которую сверху при помощи пружин крепится подвижная металлическая столешница с ограждением по периметру. К станине ниже столешницы крепится вибратор.
Плитка должна состоять из двух слоев. Лицевой первый слой задает характеристики прочности и внешний вид, а второй определяет необходимую толщину изделия. Если нужна цветная плитка, то для первого лицевого слоя используют бетонную смесь с красящими пигментами.
Этапы процесса формования:
Режим твердения изделий
Твердение (тепловлажностная обработка) изделий следует проводить при температуре не выше 70°С в мягком режиме твердения. Предельная скорость повышения и понижения температуры – не более 25°C в час.
Формы с продукцией перекладываются на поддоны слоями, каждый слой переложить листом пластика по размеру поддона, количество слоев от трех до десяти. Высота слоев зависит от прочности материала формы. На небольших производствах формы укладывают друг на друга штабелями высотой до 10 единиц. Слоеный «пирог» на поддоне перевозится в отведенное для сушки помещение. Поддоны укладывают на ровную чистую поверхность без уклона. Уклон в 1-2 градуса нарушит геометрические формы твердеющих плиток. Поддоны сверху накрыть (штабеля укутать) полиэтиленовой пленкой защитив от высыхания. Поддоны с формами нельзя передвигать ранее, чем пройдет положенное по технологии время твердения (18-48 часов после процесса заливки). Время твердения продукции зависит от температуры помещения и использованных добавок.
Отпуск готовых плит возможен при остижении изделиями 90% прочности в зимнее время года, и 70% - в летний период. Зимой, как правило, ждут 25-28 дней, летом – приблизительно 7 дней с момента изготовления
29/03/2015, 09:03