Для выполнения замеров различных деталей машин и другого оборудования применяются специальные инструменты. Приемы и методы использования таких устройств, а также точность измерений зависят от назначения измерительных средств и их конструктивных особенностей. Например, для одних изделий можно использовать обычную масштабную линейку, тогда как другие детали требуют применения более точных приборов, позволяющих замерить нужный параметр с максимальной погрешностью не более 0,01 миллиметра.
Если взять для измерения диаметра одного изделия штангенциркуль, линейку или микрометр, в каждом случае получатся различные показатели. Таким свойством обладают не только устройства для линейных замеров – угловые измерительные инструменты тоже имеют различные величины погрешностей.
Регламентирование размеров погрешностей, допустимых при проведении линейных и угловых измерений, отражено в соответствующих ГОСТах. Для деталей с линейными размерами до 50 см разрешенные погрешности должны соотноситься с такими параметрами, как допуск изделий и их номинальные габариты. Кроме того, рассчитывая максимальную величину погрешности замеров, нужно учесть методику измерения, погрешность самого инструмента, возможность температурной деформации детали и другие факторы. В случае, когда погрешность не превышает допустимых пределов, результаты измерений принимаются как верные. Таким образом, при выборе инструмента нужно учитывать следующие факторы:
- погрешность измерительного устройства;
- метод измерений;
- номинальный размер детали;
- квалитет (класс точности изделия);
- влияние температуры.
Классификация угловых измерительных средств
К основным видам инструментов для замера углов, радиусов, конусов, резьбы деталей относятся:
- угломеры;
- шаблоны;
- резьбомеры;
- штангензубомеры.
Универсальный угломер используется для проведения замеров внутренних и наружных углов различных изделий. Конструкция инструмента показана на рис. №1:
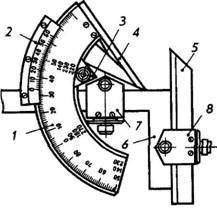
Рисунок №1
- 1 – дуга с основной шкалой;
- 2 – нониус;
- 3 – крепление нониуса;
- 4 – линейка, скрепленная с основанием;
- 5 – съемная линейка;
- 6 – угольник;
- 7 и 8 – державки.
Разметка основной шкалы имеет деления всего лишь на 130°, но, поменяв способ установки конструктивных элементов инструмента, можно измерять углы величиной до 320°. Измерения проводятся по принципу штангенинструментов – с использованием шкал основания и нониуса (для отсчета градусов применяется основание, для минут – нониус). Причем нужно учитывать, что точность отсчета минут имеет показатель 2'.
С помощью рис. №2 можно понять, как рассчитать окончательную величину угла. Между 76 и 77° основной шкалы стоит «0» нониуса, штрих шкалы основания совпадает с нониусом на отметке «9». По основанию берем наименьший показатель 76°, по нониусу учитываем точность отсчета минут – 9 х 2' = 18'. Таким образом, величина угла равна 76°18'.
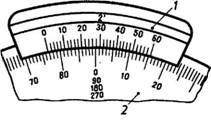
Рисунок №2
Метрический резьбомер используется для измерения шага цилиндрической резьбы. Конструктивно резьбомер – это набор пластинчатых шаблонов (рис. №3). Измерительная часть пластин представляет собой стандартный резьбовой профиль, где на одном дюйме расположен шаг определенного размера или нужное число нитей резьбы. Тип резьбомеров маркируется при помощи клейма (в данном случае это «М60°» и «Д55°»).
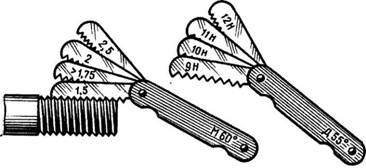
Рисунок №3
Чтобы измерить шаг резьбы, достаточно подобрать шаблон с зубцами, совпадающими с впадинами детали. Размер резьбы определяется по указанному на пластине шагу или по количеству нитей, расположенных на 1 дюйме резьбы.
Также диаметры резьбы в отверстиях или на стержнях можно узнать при помощи штангенциркуля и специальных таблиц. Инструментом определяется величина диаметра, а точное значение резьбы подбирается по таблице.
Радиусные шаблоны (профильные калибры) применяются для проверки соответствия деталей сложного профиля определенным шаблонам. Такие инструменты чаще всего используются в машиностроении и в других сложных производствах. Проверка проводится методом совмещения детали и шаблонного профиля – при этом просвет между изделием и измерительной кромкой шаблона должен находиться в рамках допустимых величин.
Конструкция шаблона показана на рис. №4. В состав инструмента входят стальные пластины с закругленными концами, на которых указаны размеры радиусов. В данном случае в комплект инструмента входят шаблоны с радиусом от 1 до 6,5 мм, но промышленные радиусомеры могут иметь пластины больших размеров.
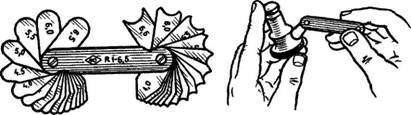
Рисунок №4
Штангензубомеры используются для измерения зубчатых колес. Составные части устройства представлены на рис. №5:
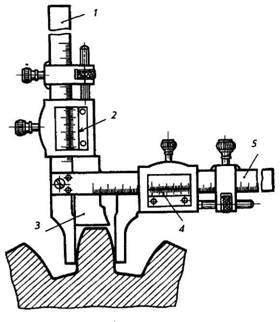
Рисунок №5
- 1 – вертикальная линейка для выставления высоты;
- 2 – нониус;
- 3 – упор;
- 4 – шкала нониуса;
- 5 – горизонтальная линейка для промера толщины зубьев.
Чтобы провести измерения, нужно выставить упор на необходимую высоту и зафиксировать его крепежным элементом. Затем упор ставится поверх зуба, а губки горизонтальной линейки подводятся к профилю зуба. Толщина зуба замеряется с помощью нониуса (отсчет выполняется по тому же принципу, что и на штангенциркуле).
Результат каждого измерения имеет определенную точность обмера, то есть включает в себя отклонение от истинного размера изделия. Если точность обмера составляет +/- 1, это значит, что величина погрешности (в ту или другую сторону) не превышает 0,01 мм. На практике такое определение точности обмера применяется редко, так что подходящий вид измерительного инструмента подбирается, исходя из размеров допусков, указанных на чертежах.
Контроль качества деталей в условиях производства выполняется с помощью специальных приборов, которые проверяют размеры изделий прямо во время изготовления. Сегодня вместо механических измерительных инструментов и автоматов с электроконтактными датчиками все чаще используются цифровые контрольные устройства, выполняющие наиболее точные измерения.
Измерительные инструменты
Для выполнения замеров различных деталей машин и другого оборудования применяются специальные инструменты. Приемы и методы использования таких устройств, а также точность измерений зависят от назначения измерительных средств и их конструктивных особенностей. Например, для одних изделий можно использовать обычную масштабную линейку, тогда как другие детали требуют применения более точных приборов, позволяющих замерить нужный параметр с максимальной погрешностью не более 0,01 миллиметра.
Если взять для измерения диаметра одного изделия штангенциркуль, линейку или микрометр, в каждом случае получатся различные показатели. Таким свойством обладают не только устройства для линейных замеров – угловые измерительные инструменты тоже имеют различные величины погрешностей.
Регламентирование размеров погрешностей, допустимых при проведении линейных и угловых измерений, отражено в соответствующих ГОСТах. Для деталей с линейными размерами до 50 см разрешенные погрешности должны соотноситься с такими параметрами, как допуск изделий и их номинальные габариты. Кроме того, рассчитывая максимальную величину погрешности замеров, нужно учесть методику измерения, погрешность самого инструмента, возможность температурной деформации детали и другие факторы. В случае, когда погрешность не превышает допустимых пределов, результаты измерений принимаются как верные. Таким образом, при выборе инструмента нужно учитывать следующие факторы:
К основным видам инструментов для замера углов, радиусов, конусов, резьбы деталей относятся:
Универсальный угломер используется для проведения замеров внутренних и наружных углов различных изделий. Конструкция инструмента показана на рис. №1:
Рисунок №1
Разметка основной шкалы имеет деления всего лишь на 130°, но, поменяв способ установки конструктивных элементов инструмента, можно измерять углы величиной до 320°. Измерения проводятся по принципу штангенинструментов – с использованием шкал основания и нониуса (для отсчета градусов применяется основание, для минут – нониус). Причем нужно учитывать, что точность отсчета минут имеет показатель 2'.
С помощью рис. №2 можно понять, как рассчитать окончательную величину угла. Между 76 и 77° основной шкалы стоит «0» нониуса, штрих шкалы основания совпадает с нониусом на отметке «9». По основанию берем наименьший показатель 76°, по нониусу учитываем точность отсчета минут – 9 х 2' = 18'. Таким образом, величина угла равна 76°18'.
Рисунок №2
Метрический резьбомер используется для измерения шага цилиндрической резьбы. Конструктивно резьбомер – это набор пластинчатых шаблонов (рис. №3). Измерительная часть пластин представляет собой стандартный резьбовой профиль, где на одном дюйме расположен шаг определенного размера или нужное число нитей резьбы. Тип резьбомеров маркируется при помощи клейма (в данном случае это «М60°» и «Д55°»).
Рисунок №3
Чтобы измерить шаг резьбы, достаточно подобрать шаблон с зубцами, совпадающими с впадинами детали. Размер резьбы определяется по указанному на пластине шагу или по количеству нитей, расположенных на 1 дюйме резьбы.
Также диаметры резьбы в отверстиях или на стержнях можно узнать при помощи штангенциркуля и специальных таблиц. Инструментом определяется величина диаметра, а точное значение резьбы подбирается по таблице.
Радиусные шаблоны (профильные калибры) применяются для проверки соответствия деталей сложного профиля определенным шаблонам. Такие инструменты чаще всего используются в машиностроении и в других сложных производствах. Проверка проводится методом совмещения детали и шаблонного профиля – при этом просвет между изделием и измерительной кромкой шаблона должен находиться в рамках допустимых величин.
Конструкция шаблона показана на рис. №4. В состав инструмента входят стальные пластины с закругленными концами, на которых указаны размеры радиусов. В данном случае в комплект инструмента входят шаблоны с радиусом от 1 до 6,5 мм, но промышленные радиусомеры могут иметь пластины больших размеров.
Рисунок №4
Штангензубомеры используются для измерения зубчатых колес. Составные части устройства представлены на рис. №5:
Рисунок №5
Чтобы провести измерения, нужно выставить упор на необходимую высоту и зафиксировать его крепежным элементом. Затем упор ставится поверх зуба, а губки горизонтальной линейки подводятся к профилю зуба. Толщина зуба замеряется с помощью нониуса (отсчет выполняется по тому же принципу, что и на штангенциркуле).
Результат каждого измерения имеет определенную точность обмера, то есть включает в себя отклонение от истинного размера изделия. Если точность обмера составляет +/- 1, это значит, что величина погрешности (в ту или другую сторону) не превышает 0,01 мм. На практике такое определение точности обмера применяется редко, так что подходящий вид измерительного инструмента подбирается, исходя из размеров допусков, указанных на чертежах.
Контроль качества деталей в условиях производства выполняется с помощью специальных приборов, которые проверяют размеры изделий прямо во время изготовления. Сегодня вместо механических измерительных инструментов и автоматов с электроконтактными датчиками все чаще используются цифровые контрольные устройства, выполняющие наиболее точные измерения.
19/03/2015, 05:03